HOT ROLLING
In CAESA we produce hot rolled special profiles with a maximum width of 110 mm for all type of sectors and industries. These profiles are always produced according to the drawings and the specific needs of each customer.
We were founded in 1946 and are specialists in the steel transformation sector. We have a long national and international business experience. We know the market and the current demands of the different industry sectors and we offer tailor made solutions.
In order to produce the profiles in an accurate and efficient way, we have an expert design and technical team, a laboratory, our own tool development and innovating machinery, as well as several specialized production lines.
Hot rolled profiles in steel
Our delivery dates are agile and adapted to each customer.
In order to be able to prepare a feasibility study, we need to receive the following technical information:
- Drawing and specifications of the profile to be produced.
- Steel grade required.
- Annual consumption.
Our team also offers specialized advice to each customer, drawing proposals and also technical recommendations when we develop new steel profiles.
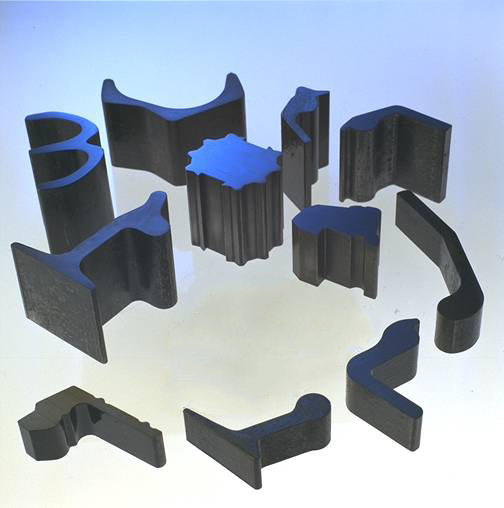
Hot rolling process
The hot rolled profiles are the result of shaping the steel raw material, square shaped billet by reduction.
After cutting the billet to a specific length, it undergoes a warmup process in the oven at high temperatures. Then it is descaled with water pressure and then deformed with different passes through several casting tools in our hot rolling lines until we reach the desired final shape. This profile is cooled down and then straightened and cut to the cusomer specified length and the profile is finally deburred.
Our tailor made profiles can be obtained in different lengths, dimensions and carbon steel grades.
Once we have the profile required by the customer in bars, we can also add some other processes like the saw cutting into pieces or the shot blasting to improve the surface aspect of the hot rolled product.
Hot rolled profiles advantages
The use of special profiles offers benefits and advantages to the customer.
Main competitive points of the use of special profiles versus standard materials:
- Reduces the customer processes, lowering its costs:
- Materials designed according to the customer requirements (Steel grade, shapes, lengths…)
- It improves the customer’s productivity, reducing the machining processes, the tool wearing and consequently their final costs.
- Lower raw material costs as with special profiles, less steel is used than with simple standard material (rounds, squares, flat bars, among others).
- Personalized design, unique profiles for each customer.
High resistance
Economics
Different shapes
Characteristics of the hot rolled profiles in steel
Tolerance: +/-0,3 mm.
Straightening: 1,5 mm/meter.
Rugosity: Ra 6,3-12.
Special sections between 200 and 2.500 mm2 (1,5 to 20 Kg/lineal meter).
Maximum width 110 mm.
Non alloyed and alloyed steels.
Used machinery for the hot rolling process
At CAESA we bet on innovation and the development using precise equipment and applying continuous improvement systems.
With this target we count with the following machinery park:
- 2 shears and 2 saws for cold cutting billets up to 150mm.
- 1 pusher furnace for billet heating with 10 mt/h capacity.
- 1 galloping furnace for billet heating with 10 mt/h capacity.
- 1 billet roughing train for dimensions up to 150mm.
- 3 hot rolling lines with 280mm between centres.
- 2 cutting and straightening lines.
- 1 straightening machine.
- 2 deburring lines.
- 4 disk saws for cutting pieces and bundles.
Shared machinery with the cold drawing process
Some facilities and processes are also used in both technologies, hot rolling and cold drawing.
- 10 bridge cranes with a capacity between 5 and 10 mt.
- 2 design and tool machining equipment (CAD/CAM).
- 3 CNC Turning machines for tool construction.